News
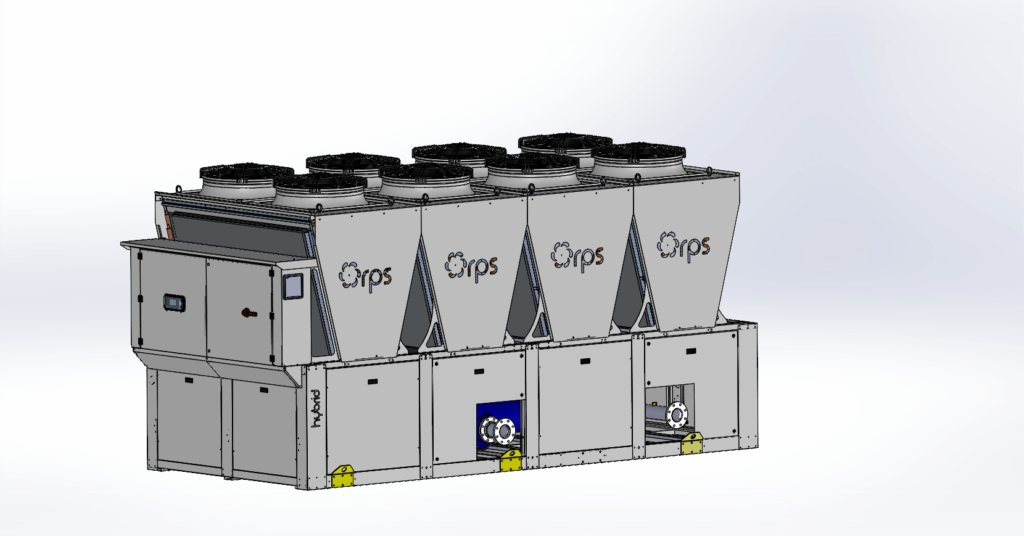
JAN 2024
NEW HYBRID DESIGN
RPS COOLING has developped a new HYBRID range, air cooled chiller range covering up 900 kW capacity in different working configurations (integrated freecooling) and refrigerant gas (R454B-R32-R513A).
Also available with natural refrigerant gas R290.
19 models have been designed through preassembled modules in order to improve the production timing.
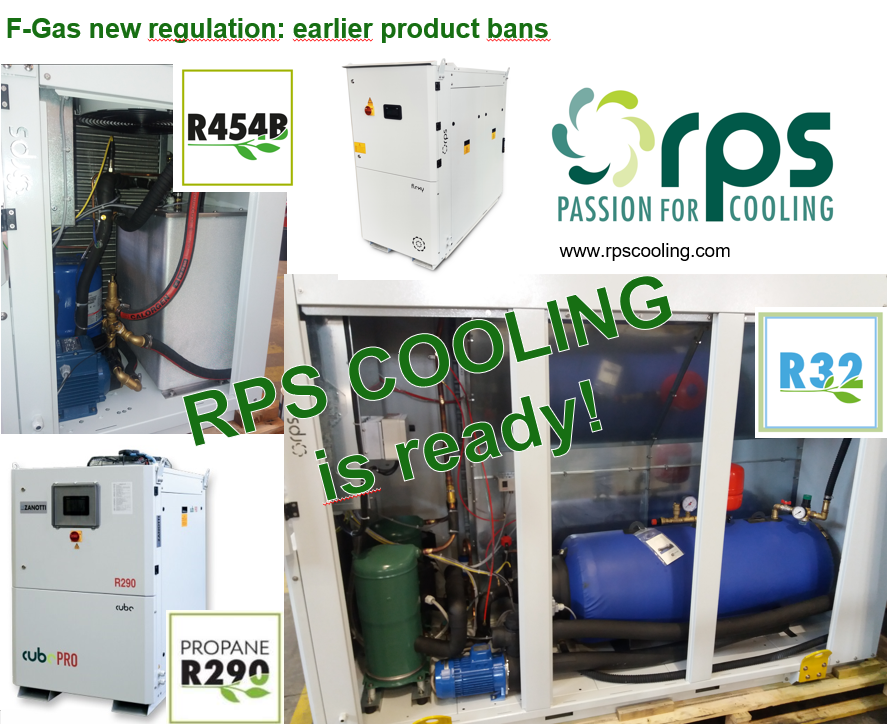
30 March 2023
New F-Gas regulation: RPS COOLING is ready
The HVACR industry faces a tough new HFC phase down timetable and earlier product bans in new F-gas regulation revision proposals voted by the European members.
RPS COOLING already developped some ranges able to apply for this new standard because of the use of natural gas and /or low GWP refrigerant gases

Feb 2022
RPS COOLING open a new facility in UK.
Located close to Leicester, it provides an excellent strategic hub to support its growing customer base in the UK

SIFA 2021 EXHIBITION IN PARIS - RPS COOLING FRANCE - 16/18 Nov
First Exhibition of our branch office in Paris for Comfort and Refrigeration


1 MW capacity with R449A at -10°C water leaving temperature
A new interesting installation for food application was made by our branch office in France with 2 modules for 1 MW total capacity with 100% heat recovery (700 kW)

HYBRID 250 kW capacity for air conditioning
Air cooled water chiller with R410 refrigerant gas, 860.000 Btu/h, with double 5bar pumps, shell & tube evaporator, 4 scroll compressors in 2 separate circuits – according to UL508A standards

Propane R290 gas heat pump 200 kW capacity
New propane R290 gas air cooled chiller in reversible heat mode 200 kW capacity
for air conditioning and process coolign application

July 2020 – RPS COOLING open a new sister company in FRANCE


PROPYLENE R1270 CHILLER WITH NATURAL GAS
RPS COOLING has produced and installed a 50 kW capacity air cooled water chiller with 5 kg of naturale gas R1270 (PROPYLENE) with 2 BITZER comp with -10°C evaporating temp.

CONDENSING UNIT WITH INVERTER DRIVEN COMPRESSOR FOR VERY LOW WATER TEMP -42°C FOR OIL & GAS APPLICATION
RPS COOLING has designed and produced a condensing unit for 7 kW, evaporating temperature -47°C, inverter driven BITZER compressor, with R448A refrigerant gas for an oil & gas application.


R1234ZE CHILLER WITH SCREW COMPRESSORS FOR FOOD APPLICATION


2 MW PROPANE CHILLERS FOR FOOD APPLICATION

CONDENSERLESS LIQUID CHILLER, COMBY RANGE


PROPANE LIQUID CHILLERS FOR FOOD APPLICATION

RPS AT INTERLIFT 2017 AUGSBURG 17-20 OCTOBER
RPS CHILL THE AUTOMOTIVE INDUSTRY (PRESS RELEASE)
lt is a model of the chiller range”Hybrid” for an installation in Germany. These coolers are suitable for cooling glycol water for industrial processes. They are compact chillers, multi-Scroll circuit with inverter technology with continuous capacity of power with an important energy saving; With electronic EC fans, electronic thermostatic valves. Hydraulic module on board, with storage tank and centrifugal recirculation pump.
Is important to highlight the high technological content of our machines, where electronics are increasingly predominant, in favour of a high energy saving compared to a traditional on-off operation of the compressors. The inverter technology for the compressors makes the thermoregulation + effective in the face of an important reduction of the electrical consumption, especially at partial loads.
The control unit of the chiller, equipped with a 4.3 “LCD colour display, manages the temperature of the fluid. Alarm signals are reported immediately through a serial communication in Modbus between the chiller and the press system. An intranet connection allows you to monitor the operation, or any anomalies, remotely.
This cooler has been commissioned by our Spanish client, manufacturer of large mechanical presses for the printing of automotive components. The purpose was to provide a constant temperature of a glycol water at 23 °c with a precision of +/-1 °C, and a cooling capacity of 400 kW. The important inertial accumulation of the chiller has been sized to compensate for the thermal load peaks due to the sudden and non-constant cycle work. The cooled water goes to thermoregulation the temperature of two large Siemens engines applied to our customer’s printing machine. The fluid through the ducts in the motor itself maintains the mechanical part. Any overtemperature, and consequent thermal expansion of the metallic materials, cause failure in the printing process where the precisions in the game of the printed artefact are at a hundredth of micron.
The final installation took place in northern Germany at the German plant of an international group leader in the production of automotive components (such as steel frames, body parts, metal components,…).


R290 PROPANE WATER CHILLERS

R407F SCREW LOW WATER CHILLER

IMTS CHICAGO
